Businesses that ship products to customers or other companies will require some level of warehousing. The warehousing required could offer storing and managing fulfillment for anything from large pallets to individual eCommerce sales. It could also offer other services if the business has specific needs.
No matter your business type or what you are selling, you will require some level of warehousing and fulfillment—and with that comes warehousing costs. Here is a breakdown of how warehousing costs work and what influences the price you pay for your fulfillment needs.
What are Warehousing Costs and How Are They Calculated?
Warehousing costs are the fees businesses pay to a fulfillment company to cover warehousing expenses. These costs will vary greatly depending on a number of factors, including the amount of space you are renting in the warehouse and what special accommodations the warehouse offers.
Warehousing costs are calculated based on the business’s need and use of the warehouse, as well as the expenses a warehouse must account for, like paying their employees and covering utility bills. For this reason, warehousing costs tend to vary greatly depending on where the located and what it is you are storing there, among other things.
What is Included in Warehousing Costs?
Warehousing costs account for a number of factors, but generally can be broken down into two basic categories:
Rent
The first part of your warehousing fees is your rent. This is often based on the square footage within the warehouse that your products will require. It can also be based on the number of items you are storing, especially for smaller items that don’t take up a lot of space.
NNN/CAM Charges
Also known as “Additional Occupancy Expenses,” NNN/CAM charges exist to cover everything else that isn’t accounted for in your rent, such as utilities and taxes. Utilities also may be charged separately from these charges or rent, depending on how the landlord decides to set up your warehousing costs.
What Will Influence My Warehousing Costs?
The actual costs a business will pay for warehousing vary significantly. The price per product or square foot will be different depending on several factors, some of which may be outside of your control.
Warehouse Location
Warehouse locations greatly impact warehousing costs, as certain areas may be more competitive than others. They will also be under different state and local tax laws and regulations that influence what is ultimately charged to businesses renting warehouse space.
Facility Type
Although you may be limited in location options, you do have more say over the type of warehouse you opt to use. Certain warehouse facilities, such as those with temperature-controlled warehouses built for cold storage, may be more expensive. If your warehouse includes any level of automation or fulfillment on your behalf, this will also increase the costs in exchange for a higher level of logistics management.
Technology
Automated systems will inevitably cost more than a standard warehouse, but they often make up for it by streamlining your processes to reduce your overall fulfillment costs. Sophisticated analytics and tracking can help improve efficiency and reduce errors in your fulfillment process, leading to more satisfied customers and a better experience overall.
Labor Costs
Any warehouse will involve some level of labor costs to pay a fair wage to employees. These costs are factored into your rent, which covers both the physical space and the labor required to maintain and manage it.
Security and Insurance
While better insurance and heightened security may result in higher costs for one warehouse versus one with minimal insurance and security, the extra expense is well worth it to keep your business protected.
How Can I Decrease My Warehousing Costs?
While warehousing costs are inevitable, there are a few strategies you can implement to keep the costs as low as possible without sacrificing quality warehousing for your business.
Avoid Overstocking
Keeping track of how much inventory you actually need, and strategically planning lead time, can help you prevent overstocking your inventory in a warehouse, which can cause you to pay a lot more for warehouse space you don’t actually need.
Keep Inventory Flowing
If you have control over where and how your inventory is set up within your warehouse, try to set it up in a way that puts fast-moving inventory at the front of the warehouse where you can access it easier to keep it flowing in and out of the warehouse. Accurate demand forecasting can also help.
Work with a 3PL
The best way to decrease your warehousing costs is to choose a 3PL for your warehousing, combining fulfillment and logistics with storage. This will also speed up the process of shipping products out to customers from the warehouse, and a fulfillment center with excellent automation and tracking will be able to stay on top of your replenishment to keep your business moving in both the slow and busy seasons.
At Smart Warehousing, we’ve got you covered when it comes to warehousing. With warehouses across the country, we put our clients closer to the customer to ease the strain of last-mile delivery with 12 million square feet of warehouse space nationwide. Paired with our proprietary warehouse management software to give you all the visibility you need to keep track of all orders and inventory moving in and out of the warehouse, we’re your one-stop shop for end-to-end coverage on your supply chain. Contact us to get started with a free quote!
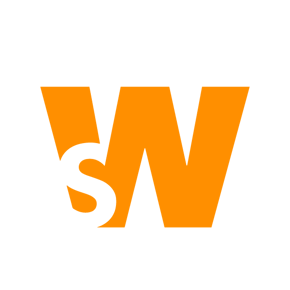