How much inventory should you have on hand? It’s easy to wrestle with this question when you have a steady stream of orders and shipping deadlines to meet. Without an answer, you can have too much inventory sitting on the shelves, driving up your costs. Or you may end up with just the opposite, causing fulfillment delays and frustrated customers while you seek to replenish your stock. So how can you calculate just the right amount?
There are a few different strategies you can consider, but we recommend starting with this foundational one: calculating average inventory.
What is Average Inventory?
Average inventory is a basic inventory management calculation that allows you to determine your average inventory over a specific period of time. If this sounds straightforward, it is. It’s an easy way to determine how much inventory your business is likely to have in stock over a given month, quarter, and so on. Calculating average inventory can give you a strong foundation to determine how much product to order when the time is right to restock.
Calculating Average Inventory: What’s Involved
To properly calculate average inventory, you first need to know your beginning and ending inventory levels over a given time period. Most inventory managers will calculate average inventory for a specific month of the year, for example.
To determine your beginning inventory calculation in this example, find out the value of inventory you had on hand at the end of the previous month. Then, to calculate your ending inventory, take that beginning inventory number and add the amount of additional inventory purchased in the current month. Subtract the cost of goods sold that month from this new total, and then you’ll have your ending inventory value.
Now you are ready to calculate your average inventory for the month. Add the beginning inventory and the ending inventory together, then divide that sum by two. You’ll have your average inventory.
You have the flexibility to calculate average inventory over other time periods as well. If you want to determine your average inventory for the quarter, for example, add your beginning inventory for the quarter with the ending inventory values for each of the three months in the quarter. Then divide this total sum by four, and you’ll have the average inventory for the quarter.
In summary, the formula for calculating your average inventory will always look like this:
(Beginning Inventory + Ending Inventory) / Time Period = Average Inventory Calculation
The Pros and Cons of Average Inventory Calculations
Calculating average inventory can be a powerful tool for better understanding and managing your product supply. But before you utilize this strategy, it is important to consider the pros and cons.
The Pros:
Future Inventory Planning: With clarity on your average inventory levels during a given period of time, you can use this information to plan your future supply needs. This means you can order products based on actual averages instead of guessing. And you can adjust your average inventory calculations to reflect your ordering frequency for further precision.
Additional Data Metrics: As you dive deeper into inventory management, you can use your average inventory calculation in these additional formulas, giving you further insight:
- Inventory Turnover Ratio: How often you turn over your entire inventory
- Average Inventory Period: How many days it takes to sell your entire inventory
With these numbers, you can determine which products are selling well and restock accordingly. You can also target slower products with strategic discounts and additional marketing efforts.
The Cons:
Seasonal Changes: As with most businesses, there are certain seasons when you go through inventory faster than others. And certain products may only sell at specific times of the year and require higher inventory levels during those times. Calculating average inventory may be less helpful when you plan to have large amounts of product for a limited time and then nearly none at all after the season ends.
Price Differences and Outside Variables: As you calculate average inventory, higher-priced items may skew your inventory values, making it harder to differentiate the impact between specific products. Also, your average inventory gives you a limited picture of all the variables you need to consider for inventory management. It won’t account for outside influences such as industry challenges, the current economy, or your competitors’ tactics.
Answering the Bigger Question: Inventory Management
While calculating average inventory can clarify your inventory history and help you determine future supply needs, this is only one piece of the total inventory management puzzle. At Smart Warehousing, we can help you take control of your entire supply chain, from warehousing and replenishment to logistics and fulfillment. This means inventory peace of mind for you, and more loyalty from your customers. Contact us today to discuss your inventory management needs.
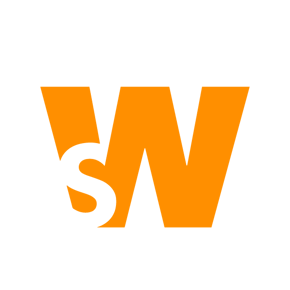