Choosing a Fulfillment Center Location
When selecting a fulfillment center to partner with for managing your business’s supply chain, one of the most important things to consider is the location of the warehouse (or warehouses) in relation to your business, your customers, and your carriers. Having the right location to stage products and fulfill orders can make the difference between rapid shipping at reasonable prices and leaving your customers wondering where their orders are while staring down a hefty shipping fee.
To help you make the best decision regarding fulfillment center locations, let’s discuss how warehouse locations might affect your order fulfillment process.
Understanding the Role of a 3PL in Fulfillment
A third-party logistics provider, or 3PL, manages the supply chain on behalf of a business, and that includes all things fulfillment. Outsourcing your organization’s fulfillment processes to a 3PL makes it easier to ship orders on demand by staging products in ideal locations relative to your customers.
The right 3PL will go beyond simple order fulfillment, bringing extensive logistics expertise to better keep up with your customer demands and maintain inventory transparency. They can also often handle distributed inventory to guarantee your products are always stocked at every fulfillment center location.
Warehouse Locations and Your Business
A common misconception regarding fulfillment centers is assuming they need to be located near your business or your manufacturing plant. But this is not as important as you might think. Just because your business or manufacturing is based in a certain metro area doesn’t mean your fulfillment center needs to be.
Although working with a warehouse near you may reduce the cost of shipping products from your location to the warehouse, it’s more financially and strategically beneficial to think about your fulfillment center’s location relative to the final destination. In other words, focus more on the last-mile delivery than transporting your products to the warehouse.
Warehouse Locations and Your Customers
Because last-mile carriers calculate costs based on eight shipping zones in the United States, the distance between the origin (fulfillment center) zip code and the destination (recipient) zip code should be as short as possible. Most last-mile carriers, including UPS, USPS, and FedEx, use the following shipping zones:
Zone 1 |
50 mile radius |
Zone 2 |
51-150 mile radius |
Zone 3 |
151-300 mile radius |
Zone 4 |
301-600 mile radius |
Zone 5 |
601-1,000 mile radius |
Zone 6 |
1,001-1,400 mile radius |
Zone 7 |
1,401-1800 mile radius |
Zone 8 |
1,801+ mile radius |
The smaller the zone, the better your shipping times and costs, making it ideal to ship from an origin geographically near the final destination. With two-day shipping’s popularity among customers, fast shipping is essential for a positive customer experience with fulfillment.
Selecting warehouse locations and fulfillment centers located near your customers may matter more than you think. Of shoppers, 42% expect a two-day shipping option for every online purchase they make. And 88% are willing to pay for same-day (or faster) delivery services.
Staging orders as close to the end user as possible becomes even more important with cold chain management. In this case, your fulfillment centers should be cold storage facilities that are prepared to transport temperature-sensitive products in a timely manner — and a large part of this is rapid on-time delivery. It’s also important to consider whether your products are headed toward commercial or residential destinations.
Warehouse Locations and Returns
Fulfillment doesn’t just stop when a product is successfully delivered to the consumer. While the goal is to have 100% customer satisfaction, the reality is that returns are inevitable. Whether you eat the cost of returns or pass on the return shipping to your customers, it’s best to keep these costs down just as you would the initial shipping costs.
And that leads to yet another benefit of using a fulfillment center rather than a warehouse, as they are better prepared to ease the burden of returns. In most cases, returns can be made directly to your fulfillment center rather than traveling all the way back to you, increasing the value of having warehouse locations near the end user that are prepared to manage returns on your behalf, restocking or disposing of products based on quality on receipt back at the fulfillment center.
Do I Need Multiple Fulfillment Centers?
The number of fulfillment centers required depends in part on the size of your business and the products you sell. A cold chain business may need more fulfillment centers to effectively serve customers nationwide, whereas many e-commerce brands can operate on a smaller scale in the early years of their business.
Attempting to calculate and organize relationships with multiple fulfillment center providers, it is much better (and more cost-effective) to partner with a company that has a nationwide network of warehouses. Having such a vast geographic footprint will make it easier to provide rapid delivery times and effectively decrease your overall shipping costs.
How Smart Warehousing Covers Your Fulfillment Process
Not every business will have the same fulfillment needs, which is why it’s essential to have a 3PL provider that offers fulfillment services catered uniquely to you. With e-commerce fulfillment, retail fulfillment, and even B2B fulfillment options, Smart Warehousing offers end-to-end coverage that will ensure the best possible fulfillment experience for you and your customers.
Fulfillment Center Locations for Your Customers and Your Business
At Smart Warehousing, we go the extra mile to make the fulfillment process as smooth as possible for your business. Rather than worrying about getting your products to a warehouse across the country, simply ship your inventory to our closest fulfillment location in relation to you or your manufacturer. Our software will guide distribution from there to ensure your products are staged close to customer demand.
Fulfillment Done the Smart Way
Bringing our customers a nationwide network of over 30 warehouses, we can provide 1-2 day shipping to all corners of the nation. That, coupled with the discounted rates we pass onto you from major carriers, means you will always have the most reliable and best-priced shipping for your business.
Are you ready to experience the difference having such a robust fulfillment center provider can make? Connect with one of our fulfillment consultants today to learn more about the Smart Difference.
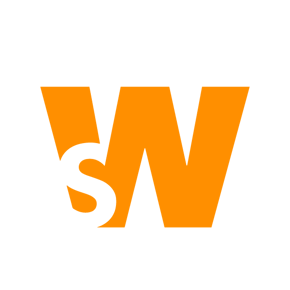